MRP – planowanie zapotrzebowania materiałowego – Co to?
- Opublikowano
- 5 min czytania
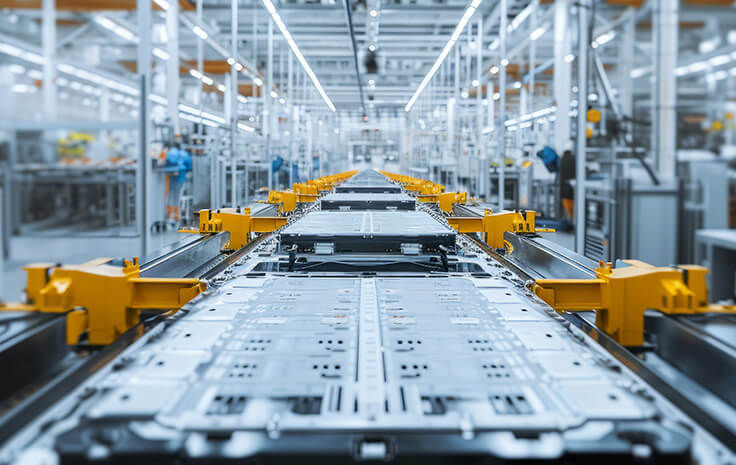
Spis treści:
MRP (z ang. Material Requirements Planning) to zbiór procesów zmierzających do optymalnego planowania zapotrzebowania materiałowego na podstawie danych z produkcji/magazynu (BOM, harmonogram produkcji, stany magazynowe).
W latach 60. ubiegłego wieku systemy informatyczne MRP zapoczątkowały informatyzację obszaru zarządzania produkcją przedsiębiorstw, które mogły dzięki komputerom zwiększyć wydajność i precyzyjność swojej produkcji. Z czasem MRP stały się częścią zintegrowanych systemów zarządzania przedsiębiorstwem ERP, gdzie następuje wymiana danych między wszystkimi kluczowymi działami przedsiębiorstwa (sprzedaż, produkcja, magazyn, księgowość, kadry).
MRP – istota działania
Sama koncepcja MRP jest nadal żywa i pomaga przedsiębiorstwom w dzisiejszej rzeczywistości gospodarczej. Jej główny cel to zapewnienie odpowiednich zapasów materiałów i półproduktów, aby zrealizować aktualną i przyszłą produkcję. Nowoczesne narzędzia MRP determinują jednocześnie w jakiej ilości i terminie należy realizować produkcję, gdyż analizują procesy w całym przedsiębiorstwie oraz współpracują z rozwiązaniami planowania i harmonogramowania (tzw. zintegrowana pętla MRP).
Jak obliczamy MRP?
Mechanizm MRP analizuje cztery kluczowe elementy:
BOM (dokładna ilość materiałów i półproduktów koniecznych do wyprodukowania wyrobu gotowego, w tym również określenie alternatywnych zamienników), harmonogram produkcji (terminy zadań produkcyjnych wynikające z zaplanowanych zleceń produkcyjnych), stany magazynowe materiałów i półproduktów oraz stany zamówień w toku (wygenerowane już wcześniej zamówienia zakupu na wymagane materiały).
W oparciu o powyższe informacje mechanizm MRP określa, w jakim terminie na produkcję powinien zostać dostarczony dany surowiec/materiał. Ta informacja zostaje uszczegółowiona o planowany czas realizacji zamówienia przez dostawcę (np. 10 dni od daty złożenia zamówienia), gdyż wtedy faktycznie dział zakupów może określić z jakim wyprzedzeniem należy złożyć zamówienie zakupu.
Dawna koncepcja MRP dążyła do utrzymania jak najniższego poziomu materiałów i produktów. Ze względu na coraz częstsze przypadki załamania łańcuchów dostaw, obecnie przedsiębiorstwa utrzymują wysokie stany minimalne kluczowych surowców, co wpływa bezpośrednio na obliczenia mechanizmu MRP, aby zapewnić odpowiedni zapas na magazynie.
Wyznacznikiem zapotrzebowania materiałowego nie muszą być tylko zaplanowane zlecenia produkcyjne wygenerowane w systemie ERP, które określają bazowe zapotrzebowanie materiałowe i wymagany ich czas dostarczenia, ale również prognozy sprzedaży, które określają nam potencjał przyszłej produkcji. Jest to w szczególności istotne, gdy lead time (kres od momentu złożenia zamówienia do chwili dostarczenia go na produkcję) dostawy surowców jest czasochłonny (np. kilka miesięcy). Wtedy prognozy podaży i pobytu są podstawowym wyznacznikiem MRP.
Wpływ MRP na planowanie produkcji
Zintegrowana pętla MRP determinuje również plan produkcji. W przypadku, gdy w wyniku określenia terminów realizacji zaopatrzenia okaże się, że są one zbyt późne, aby zrealizować zlecenie produkcyjne w wyznaczonym czasie, należy dokonać przeplanowania produkcji lub szukać na rynku alternatywnych surowców, które można dostarczyć w szybszym terminie. W tym zakresie istotna jest również ciągła analiza i szybkie reagowanie na zmiany zachodzące w otoczeniu (np. opóźnienie dostawy zamówionych materiałów), co może mieć wpływ na kontrolę realizacji poszczególnych etapów produkcji.
MRP w współczesnej erze cyfryzacji
Współczesne mechanizmy MRP korzystają z informacji, które dostarczają nowoczesne technologie jak IoT (zbieranie danych o realizacji produkcji i zużyciu surowców bezpośrednio z maszyn produkcyjnych) oraz AI (prognozowanie popytu w oparciu o algorytmu sztucznej inteligencji, które uczą się na podstawie danych historycznych oraz wyznaczają prawdopodobny trend przyszłych zapotrzebowań). Powoduje to, że planowanie zapotrzebowania materiałowego w nowoczesnych zintegrowanych systemach ERP 5.0, jakimi są rozwiązania Comarch ERP XL czy Comarch ERP Enterprise, jest bardziej zautomatyzowane, optymalne i precyzyjne.
Skomentuj
Brak komentarzy