Panelizacja i depanelizacja obwodów drukowanych (PCB)
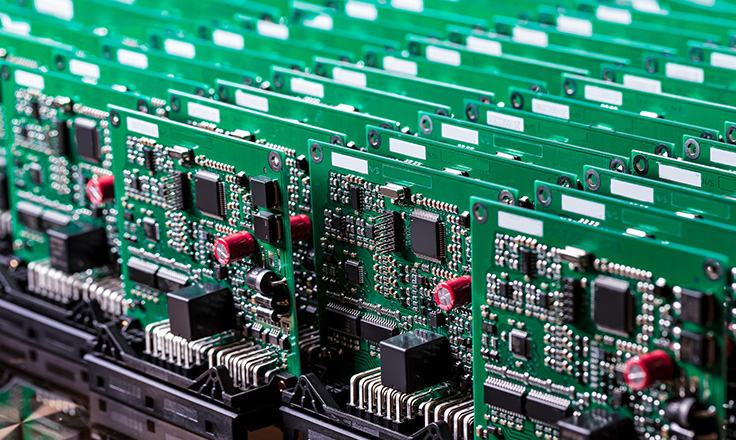
Poprawnie przeprowadzona panelizacja pakietów elektronicznych, choć często bagatelizowana, pozwala na optymalizację wszystkich procesów produkcyjnych – od montażu, przez testy, aż po późniejszą depanelizację. Dodatkowo pomaga maksymalizować efektywność wykorzystania powierzchni laminatu, a zatem – mądrzej zarządzać kosztami produkcji. Na czym polega łączenie płytek PCB w macierze oraz ich separacja? Jak prawidłowo przeprowadzić te procesy, aby uniknąć uszkodzeń obwodów? O tym wszystkim opowiadamy na przykładzie pracy Comarch IoT Plant.
Montaż SMT oraz THT, automatyczna kontrola wizualna AOI, a także testy funkcjonalne, np. przy wykorzystaniu Flying Probe – o powodzeniu wymienionych procesów produkcyjnych przesądza wiele czynników, wśród których niebagatelne znaczenie ma odpowiednio przeprowadzona panelizacja obwodów drukowanych. Umieszczenie PCB w panelu może się okazać pomocne również podczas selektywnego nanoszenia warstwy ochronnej – lakierowania.
– Przy projektowaniu panelu obwodów drukowanych muszą nam przyświecać dwa zasadnicze cele. Pierwszym jest ułatwienie i przyspieszenie procesów technologicznych, które następują po fazie projektu, czyli montażu i kontroli. Drugi cel to również ułatwienie i przyspieszenie, a dodatkowo zwiększenie bezpieczeństwa, tym razem procesu rozdzielenia panelu na pojedyncze płytki – mówi Mateusz Rosek, Inżynier Kontroli Jakości w Comarch IoT Plant.
Czym jest panelizacja obwodów drukowanych i kiedy się ją stosuje?
W ramach standardowego procesu płytki PCB projektuje się najczęściej w formie pojedynczego obwodu. Aby jednak maksymalnie wykorzystać materiał laminatu oraz zoptymalizować montaż powierzchniowy i przewlekany, indywidualne płytki są zazwyczaj układane w macierz.
– Zastosowanie multibloku jest niezbędne do wykonania montażu automatycznego na przykład w wypadku obwodów o bardzo małych wymiarach. Ułożenie płytek w panelu umożliwia dodanie marginesu technologicznego ułatwiającego proces montażu SMT i THT, a także następujące później etapy kontroli czy depanelizacji. Można wyróżnić dwa główne sposoby łączenia obwodów w macierze, rylcowanie i frezowanie – tłumaczy Mateusz Rosek.
Jakie są najczęstsze metody panelizacji płytek PCB?
Rylcowanie
Polega na nacięciu panelu po obu stronach płyty, głębokość nacięcia stanowi mniej więcej ⅓ grubości płyty. To optymalny sposób panelizacji PCB o prostych kształtach (np. prostokąt) – w takich wypadkach odpad materiału jest minimalny. W wypadku gdy płytka ma bardziej skomplikowany, nieregularny kształt, panelizacja przez rylcowanie jest wciąż możliwa, ale wymaga dodatkowej obróbki z pomocą frezowania, w ramach którego wycinane są niestandardowe kształty. Wówczas konieczne jest również oddzielenie poszczególnych płytek obwiednią, aby pozostawić miejsce dla narzędzia (frezu).
Frezowanie
Polega na wyfrezowaniu kształtu PCB w panelu w taki sposób, aby pozostawić w zależności od rozmiaru PCB od kilku do kilkunastu tzw. mostków. Są to fragmenty laminatu utrzymujące pojedyncze PCB w panelu, mające zapewnić wystarczającą sztywność do przeprowadzenia kolejnych procesów – montażu oraz kontroli. Mostki można rozdzielić na perforowane (z nawierconymi otworami) i nieperforowane.
Na czym polega depanelizacja płytek PCB?
Depenalizacja to kolejny etap procesu produkcyjnego, który opiera się na separacji macierzy obwodów drukowanych na pojedyncze płytki. Przeprowadzamy ją przy wykorzystaniu technologii, która zależy od przewidzianego w projekcie sposobu wykonanej wcześniej panelizacji.
– Separacja płytek może nastąpić w różnych fazach procesu produkcyjnego – po etapie montażu SMT lub THT, po wykonaniu testów jakościowych, a nawet przed samym montażem obwodu w docelowym urządzeniu. W Comarch IoT Plant dysponujemy narzędziami umożliwiającymi depanelizację multibloków rylcowanych i frezowanych, takimi jak CAB Maestro 2, CAB Hektor 2 czy Asys Divisio 2100 Ergo – dodaje Mateusz Rosek.
Jakie są najczęstsze metody depanelizacji płytek PCB?
Rozcięcie paneli rylcowanych przy pomocy CAB Maestro 2
Do depanelizacji macierzy rylcowanych można użyć narzędzia Maestro, które ze względu na dwa talerze tnące o regulowanym rozstawie umożliwia dopasowanie parametrów do grubości PCB. Dzięki temu można rozcinać zarówno bardzo cienkie, jak i bardzo grube laminaty. To najszybszy, a zarazem najtańszy sposób depenalizacji. Ta metoda separacji polega na przepchnięciu panelu pomiędzy talerzami tnącymi, prowadząc je przez wykonane w procesie produkcji PCB nacięcia. To sposób zalecany w wypadku obwodów drukowanych o bardzo małych rozmiarach, które przy użyciu innych narzędzi są szczególnie narażone na uszkodzenia.
– W wypadku rylcowania umieszczenie komponentów na równi z krawędzią PCB lub poza obrysem PCB bardzo utrudnia lub wręcz uniemożliwia przecięcie panelu, gdyż talerze zwyczajnie nie mogą przeciąć fragmentu laminatu, na którym znajduje się przeszkoda. Jeśli dojdzie do takiej sytuacji, jedynym sposobem na rozdzielenie płytek jest ich bardzo delikatne, ręczne wyłamanie. Pomimo zachowania najwyższej ostrożności takie działanie może skutkować uszkodzeniem PCB. Dlatego ważne jest zaprojektowanie dobrego panelu i na przykład zastosowanie wycięć w okolicach złącz, aby talerze do nich nie dochodziły, ewentualnie odstępów pomiędzy pojedynczymi płytkami – wyjaśnia Mateusz Rosek.
CAB Hektor 2
Hektor to nóż pneumatyczny służący do ręcznego wyłamywania mostków perforowanych. Depanelizowaną płytkę należy pozycjonować na podporach tak, by krawędź tnąca noża znajdowała się nad mostkiem. Narzędzie radzi sobie bez problemu z laminatami o grubości 2 mm. Podobnie jak w przypadku rylcowania problematyczne jest umiejscowienie mostków blisko złącz lub bezpośrednio pod nimi. Ze względu na długość noża konieczne jest zapewnienie minimum 12 mm pustej ścieżki frezowania, przez którą należy przełożyć nóż.
– W wypadku płytek o bardzo nieregularnych kształtach może być to trudne do osiągnięcia. W takim wypadku ułożenie płytki na podporach nie jest możliwe. Kolejnym ryzykiem jest gęste obłożenie komponentami blisko krawędzi PCB w bezpośrednim otoczeniu mostków, opieranie panelu na elementach nie jest wskazane i grozi ich uszkodzeniem. Depanelizacja przy użyciu narzędzia Hektor jest bezpieczniejsza niż frezowanie w wypadku niewielkich płytek panelizowanych na mostkach – mówi Mateusz Rosek.
Frezarka Asys Divisio 2100 Ergo
Gdy mamy do czynienia z płytkami panelizowanymi na mostkach nieperforowanych, a także tam, gdzie pomimo zastosowania perforowanych mostków nie ma podejścia dla noża depanelizatora ręcznego typu Hektor, konieczne jest wykorzystanie frezarki Divisio. Aby wyciąć płytki na frezarce, należy zacząć od przygotowania programu dla maszyny CNC. W tym celu z wybranych warstw plików Gerber generuje się plik DXF zawierający ścieżkę frezowania na warstwie rou ting, obrys całego panelu oraz pojedynczych płytek i otwory mogące przydać się do rozstawienia kołków mocujących panel w maszynie. Następnie zapisuje się kluczowe parametry, takie jak wymiary panelu, pojedynczej płytki, odstępów pomiędzy kolejnymi płytkami w osiach X i Y, a także koordynaty fiduciali.
Następnie tak przygotowany plik DXF wczytywany jest w oprogramowaniu CAM, gdzie tworzone są ścieżki frezowania mostków, a także pozycjonowanie tzw. support pinów – kołków podpierających PCB i utrzymujących je po wyfrezowaniu. Po przygotowaniu pliku generowany jest G-CODE – kod maszynowy CNC, na podstawie którego maszyna rozstawia kołki oraz wykonuje frezowanie. W kolejnym kroku w interfejsie frezarki tworzony jest nowy program dla konkretnego produktu, do którego wprowadzane są podstawowe dane, takie jak wymiary panelu, koordynaty fiduciali oraz importowany jest G-CODE.
– Po zakończeniu tworzenia programu można przystąpić do rozstawienia kołków – maszyna automatycznie pobiera je z magazynu chwytakiem podciśnieniowym i rozstawia w miejscach zapisanych w programie. Po zamocowaniu panelu na stole uruchomiona zostaje symulacja, by upewnić się, że wszystkie ścieżki cięcia przebiegają we właściwych miejscach i nie dojdzie do kolizji frezu z elementami na płytce. Jak w przypadku poprzednich metod, zaleca się odsunięcie mostków od złącz – komentuje Mateusz Rosek.
Wycinanie bardzo małych płytek stanowi wyzwanie z dwóch względów. Pierwszy to ograniczenie technologiczne spowodowane średnicą podstawy kołków. W wypadku płytek ułożonych w panelu blisko siebie trudne jest odpowiednie ułożenie kołków w sposób, który zapewni wystarczające podparcie płytek. Czasem jeden panel trzeba rozdzielić na kilka programów, by zapewnić odpowiednią ilość miejsca na rozstawienie kołków. Drugim czynnikiem jest przewód odkurzacza, który zaciąga pył powstający podczas frezowania. Podciśnienie może sprawić, że skrajnie mała płytka zostanie wessana do przewodu lub, co gorsza, zaczepi się o narzędzie i wirując razem z frezem zacznie uderzać w kolejną wycinaną płytkę, powodując jej uszkodzenie.
– W takich wypadkach, o ile zastosowana jest perforacja mostków, dobrym pomysłem jest pozostawienie jednego mostka (można też naciąć mostek, na przykład do połowy) i wyłamanie go przy użyciu depanelizatora Hektor. Alternatywą będzie bardzo ostrożne wyłamanie ręczne. Zapisany program można wczytać przy uruchomieniu kolejnej partii tego samego produktu, po czym przystąpić do depanelizacji – dodaje Mateusz Rosek.
Podsumowanie
Panelizacja obwodów drukowanych oferuje szereg zalet, takich jak optymalizacja procesów w ramach zautomatyzowanej produkcji i testowania, a wraz z nią – oszczędność czasu i obniżenie kosztów. Właściwa realizacja panelizacji PCB – od etapu projektowania, przez wybór metody, po wykonanie – musi jednak brać pod uwagę szereg czynników, które determinują bezpieczeństwo późniejszej separacji płytek w celu ich dalszego wykorzystania.
Doskonale rozumie to zespół doświadczonych inżynierów Comarch IoT Plant, który w ramach usług montażu PCBA wykorzystuje sprzęt umożliwiający depanelizację z wykorzystaniem najskuteczniejszych narzędzi. Od etapu projektowania po późniejszą realizację, naszym celem jest finalny sukces projektu. Więcej o wsparciu, które możemy zaoferować Twojej firmie, przeczytasz na głównej stronie Comarch IoT Plant.