Płytka PCB – czym jest kluczowy komponent w produkcji elektroniki
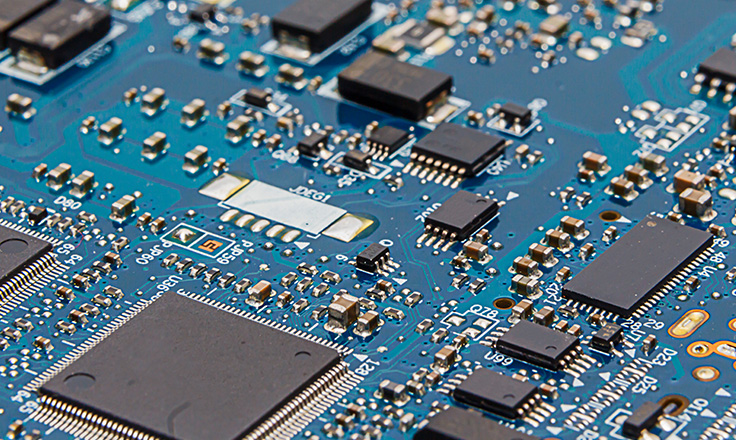
Obwody drukowane towarzyszą nam dzisiaj na każdym kroku. Są obecne w smartfonach, komputerach, sprzęcie gospodarstwa domowego, a także w urządzeniach medycznych i samolotach. W dobie miniaturyzacji elektroniki oraz rosnącego skomplikowania projektów płytek zarówno dostawcy PCB, jak i fabryki montujące na układach drukowanych wychodzą naprzeciw potrzebom klientów, oferując innowacyjne rozwiązania technologiczne oraz materiały. Jak wygląda proces zamawiania płytki PCB i montażu komponentów PCBA? Z jakimi wyzwaniami się wiąże? Odpowiedzi na te pytania dostarcza praca Comarch IoT Plant, nowoczesnej hali produkcyjnej oferującej usługi z zakresu szybkiego prototypowania i montażu urządzeń elektronicznych (EMS).
Co to jest PCB?
PCB (ang. Printed Circuit Board) to płytka obwodu drukowanego z połączeniami elektronicznymi (zwanymi także ścieżkami) oraz punktami lutowniczymi, które występują w dwóch postaciach. Pierwsza forma punktów to pady stosowane w przypadku montażu powierzchniowego, druga – otwory wykorzystywane w celu montażu przewlekanego. To na płytce PCB montowane są następnie układy elektroniczne. Wówczas mowa już o PCBA, czyli Printed Circut Board + Assembly (obwodzie drukowanym + montażu).
– Obwody drukowane zyskały popularność w drugiej połowie XX wieku, kiedy zaczęły trafiać do odbiorników radiowych. Wcześniej połączenia elektroniczne realizowane były przy pomocy przewodów, jednak tego rodzaju rozwiązanie było uciążliwe w montażu, a także – z powodu dużej liczby przewodów – kłopotliwe rozmiarowo. Pojawienie się wielowarstwowych płytek PCB pozwoliło wreszcie na tworzenie kompaktowych urządzeń o rozbudowanej funkcjonalności – tłumaczy Mateusz Rosek, Inżynier Kontroli Jakości w Comarch IoT Plant.
Budowa płytki PCB krok po kroku
Jakie są kluczowe parametry i cechy płytek drukowanych, które projektant musi zawrzeć w projekcie produkcyjnym?
Rodzaje laminatów – w zależności od przeznaczenia obwodu wykorzystujemy różne typy laminatów i materiałów. Można je kategoryzować zarówno pod względem popularności, jak i ciekawego zastosowania projektowego.
- Laminaty FR-4 – to laminat ogólnego zastosowania; od prostej elektroniki po wyroby medyczne i wojskowe, które nie narzucają wymagań dotyczących wysokich częstotliwości czy dużej pojemności cieplnej obwodu. Ten rodzaj charakteryzuje się temperaturą zeszklenia – Tg o wartości 140⁰C. Lepsze właściwości częstotliwościowe niż FR4 prezentuje laminat FR408 firmy Isola, który ma zastosowanie w obwodach radiowych.
- Laminaty typu RIGID FLEX – względnie nowy typ laminatu wśród dostępnych na rynku. Jego konstrukcja różni się od standardowej. W środku, zamiast najczęściej spotykanego rdzenia laminatu FR4 znajduje się część giętka o poliamidowym rdzeniu, na którą nałożone są folie miedziane pokryte żywicą. Następnie tak zbudowana baza obkładana jest sztywnym laminatem FR-4. Położenie warstwy FLEX może być asymetryczne – liczba warstw miedzi po obu stronach giętkiego rdzenia nie musi być jednakowa. Takie rozwiązanie pozwala na uproszczenie projektów, w których kilka płytek jest połączonych złączami. Laminaty typu FLEX cechują się elastycznością – pozwalają na wielokrotne zginanie części elastycznych bez ryzyka ich uszkodzenia
- Laminaty typu SEMI-FLEX – w odróżnieniu od laminatu RIGID-FLEX nie mamy tutaj poliamidowego rdzenia. Zgięciu ulega specjalnie przygotowana część laminatu FR-4 pokryta elastyczną soldermaską. W tym wypadku liczba cykli zginania jest mocno ograniczona. Ten typ laminatu przeznaczony jest do jednorazowego ukształtowania części giętkiej podczas montażu, np. w obudowie. Kolejne zgięcia laminatu mogą skutkować jego uszkodzeniem.
- Laminaty PTEF – to specjalistyczne laminaty typu RF, wykonane z ceramiki lub teflonu. Są przeznaczone to produkcji obwodów mikrofalowych. Wykazują najlepsze właściwości częstotliwościowe oraz najwyższą wartość temperatury zeszklenia.
- Laminaty aluminiowe i miedziane – to laminaty specjalistyczne stosowane tam, gdzie w obwodzie elektronicznym montowane są komponenty wysokiej mocy, np. tranzystory generujące duże ilości ciepła. W takim laminacie rdzeń wykonany jest z izolowanej płytki aluminiowej lub miedzianej.
- Laminaty HDI – nie wyróżniają się na tle innych zastosowaniem niekonwencjonalnego materiału – zazwyczaj są to laminaty FR-4 o lepszych właściwościach termicznych i częstotliwościowych lub laminaty firmy Isola czy Rogers. Cechują się jednak wyższym współczynnikiem Tg niż standardowe laminaty FR-4, sięgającym 185⁰C, dlatego są zalecane do wielowarstwowych projektów PCB. Warto o nich pamiętać tam, gdzie mamy do czynienia z bardzo gęstym obłożeniem komponentów na powierzchni laminatu.
Warstwy PCB – płytka PCB zbudowana jest niczym tort lub kanapka. W samym środku znajduje się rdzeń. Jest on obkładany z jednej (płytki jednowarstwowe) lub obu stron naprzemiennie warstwami folii miedzianej wytrawionej mozaiką ścieżek oraz tak zwanego prepregu – włókna kompozytowego nasączonego żywicą. Podczas produkcji PCB tak przygotowany stos warstw łączony jest w prasie pod wpływem dużego nacisku oraz wysokiej temperatury. W zależności od stopnia skomplikowania projektu wyróżniamy płytki:
- 1-warstwowe – warstwa miedzi ze ścieżkami i padami znajduje się tylko po jednej stronie laminatu,
- 2-warstwowe – warstwa miedzi ze ścieżkami i padami znajduje się po obu stronach laminatu,
- wielowarstwowe – w wypadku, gdzie obłożenie komponentów na płytce jest bardzo gęste, zwyczajnie brakuje miejsca, by poprowadzić wszystkie ścieżki na powierzchni jednej czy dwóch warstw. Takie rozwiązanie jest szczególnie popularne w wypadku zastosowania dużych układów BGA. W zależności od liczby i rodzaju zastosowanych układów liczba warstw może wynosić 4, 6 lub 8, ale zdarzają się projekty, gdzie konieczne jest zastosowanie 16, a nawet 20 warstw miedzi.
Przeznaczenie urządzenia wymusza zastosowanie konkretnych grubości warstw. Na przykład w obwodach zasilających, gdzie mają docelowo płynąć wysokie prądy, warstwy miedzi będą grubsze niż w standardowych ścieżkach sygnałowych. Grubość warstwy miedzianej wyrażana jest w uncjach (Oz) lub mikrometrach (µm). Standardowo (podczas prasowania PCB grubości zarówno foli miedzianej, jak i prepregów, mogą się nieznacznie zmniejszyć) końcowa grubość miedzianej warstwy zewnętrznej wraz z wykończeniem to 35 µm (1 Oz), tyle samo przyjmuje się dla warstw wewnętrznych. Jeśli projekt tego wymaga, grubości zarówno warstw zewnętrznych, jak i wewnętrznych, mogą zostać zwiększone np. do 70 µm, a w skrajnych przypadkach do 105 µm czy 210 µm. Możliwe jest również zmniejszenie grubości miedzi do 0.25 Oz.
– Z liczbą oraz grubością warstw wiąże się również szerokość ścieżek oraz odległości pomiędzy ścieżkami i warstwami laminatu. Te kryteria są krytyczne, by zachować określone impedancje ścieżek. To ważne ze względu na pozbycie się zakłóceń, które mogą pojawić się w obwodzie i mieć negatywny wpływ na działanie układów elektronicznych zamontowanych na laminacie – komentuje Mateusz Rosek.
Przelotki – aby połączyć dwie lub więcej warstw, konieczne jest zastosowanie przelotek (Via) pomiędzy poszczególnymi warstwami. Przelotki to otwory, których ścianki pokryte są metalizacją, dzięki czemu zapewniają połączenie elektryczne pomiędzy określonymi warstwami. Standardowe przelotki są wykonywane w technologii wiercenia, natomiast mikroprzelotki – ze względu na ograniczenia technologiczne – wykonywane są przy pomocy lasera. Wyróżniamy 7 typów przelotek (od Typu I do Typu VII), różniących się sposobem pokrycia lub wypełnienia. Warto nadmienić, że pokrycie przelotek może być jedno- lub dwustronne. Ze względu na sposób połączenia warstw możemy podzielić je na kilka głównych typów:
- Through-hole vias – przelotka przechodząca przez warstwy łączy ze sobą zewnętrzne warstwy miedzi.
- Blind vias – przelotka ślepa, łącząca ze sobą wybrane warstwy. Może być to połączenie pomiędzy warstwą zewnętrzną i wewnętrzną lub pomiędzy konkretnymi warstwami wewnętrznymi.
- Burried vias – przelotki zagrzebane łączące ze sobą warstwy wewnętrzne. W odróżnieniu od przelotek ślepych wykonanie tego rodzaju przelotek wymaga wiercenia w konkretnych warstwach laminatu.
- Mikrovias – mikroprzelotki o bardzo małej średnicy możliwe do wykonania jedynie przy użyciu lasera. Mogą występować również ślepe i zagrzebane mikroprzelotki.
- Vias In Pad – przelotki wykonane w padach, najczęściej stosuje się je, aby połączyć sygnały biegnące z układów BGA.
Pady i otwory – na tym etapie projektant PCB tworzy zewnętrzne warstwy miedzi (lub jedną zewnętrzną warstwę w wypadku płytek jednowarstwowych), na której umieszczone są: pady, czyli punkty lutownicze do powierzchniowego montażu komponentów, a także otwory – do montażu przewlekanego lub przeznaczone do pozycjonowania i montażu mechanicznego w obudowie lub docelowym miejscu montażu, np. na innej płycie PCB.
Na tym etapie bardzo ważny jest dobór wielkości i kształtów padów do użytych w projekcie komponentów. Z punktu widzenia montażu powierzchniowego ma to bardzo duży wpływ na poprawność lutowania elementów. Wykonanie na PCB footprintu (układu wyprowadzeń komponentu elektronicznego) niezgadzającego się z realnym footprintem komponentu może spowodować nieprawidłowe przylutowanie komponentu, np. powstanie tak zwanych nagrobków elementów pasywnych. Może to również uniemożliwić przylutowanie elementu na PCB. Jednakowa sytuacja wystąpi w przypadku wykonania zbyt małych padów. Zachowanie niewystarczających odległości pomiędzy padami w wypadku układów SOP, SOT, QFN czy QFP może skutkować powstaniem zwarć pomiędzy wyprowadzeniami układów.
Otwory możemy rozróżnić na:
- Plating Through Hole (PTH) – otwory z metalizacją przechodzące na wylot płytki, tworzące połączenie elektryczne pomiędzy warstwami. Służą do montażu elementów montowanych w sposób przewlekany, np. kondensatorów elektrolitycznych, przekaźników, cewek, a także różnego rodzaju złącz. W wypadku tych ostatnich warto wspomnieć o złączach typu Press-fit, w których wyprowadzenia nie są lutowane, a wciskane w metalizowane otwory. W tym wypadku krytyczna jest dokładność wykonania takich otworów, aby zapewniały trwały i prawidłowy montaż złącz.
- Non Plating Through Hole (NPTH) – otwory bez metalizacji przechodzące na wylot, nietworzące połączenia elektrycznego. Służące najczęściej do pozycjonowania komponentów na płytce PCB lub montażu samej płyty w obudowie bądź innym miejscu przeznaczenia.
Otwory mogą mieć różne kształty i rozmiary w zależności od zastosowania. Tak samo jak w wypadku padów krytyczne jest zachowanie w projekcie odpowiedniego footprintu umożliwiającego poprawny montaż komponentów.
Grubość płytki – zastosowanie dużej liczby warstw PCB, a także warstw miedzi o większej grubości, zwiększy grubość gotowego laminatu. Standardowo grubość płytki to 1,6 mm. Grubość bardziej skomplikowanych płytek to 2 mm, jednak dostawcy PCB oferują już laminaty o grubości nawet 6 mm. Zdarzają się jednak sytuacje, w których obwód drukowany ma być zamontowany w miejscu lub obudowie, gdzie standardowa płytka o grubości 1,6 mm się nie zmieści. W takich wypadkach projektant może stworzyć płytkę o grubości 1,1 mm, 0,6 mm, a nawet cieńszą. Najcieńsza płytka PCB, którą miałem w rękach w swojej karierze w IoT Plant, miała grubość 0,6 mm.
Soldermaska – to maska ochronna zabezpieczająca powierzchnię PCB zarówno przed korozją, jak i przed niekontrolowanym rozpływem stopu lutowniczego. Soldermaska pokrywa całą powierzchnię PCB z wyjątkiem padów i otworów typu PTH, a także przelotek, jeśli tak zakłada specyfikacja. Soldermaska jest aplikowana w formie ciekłej farby utwardzanej za pomocą światła UV. Przy tej okazji warto wspomnieć o masce zrywalnej, nanoszonej metodą sitodruku – peelable mask. To tak zwana maska tymczasowa, zabezpieczająca na przykład otwory lutownicze przed wypełnieniem stopem podczas procesu SMT lub THT. Po przeprowadzonym procesie lutowania taką maskę można oderwać, aby przystąpić do kolejnych etapów montażu. Maska lutownicza występuje w różnych kolorach, standardowo jednak w (najtańszym) zielonym. Na życzenie klienta fabryka może zastosować inny kolor, np. czarny, niebieski, czerwony.
Wykończenie – inaczej plating, określa materiał zabezpieczający przed korozją pady, a także inne obszary miedzi niepokryte maską lutowniczą. Różne rodzaje platingu charakteryzują się odmienną ceną, wytrzymałością, jak również wpływem na środowisko. Wśród nich wymienić możemy:
- HASL (Hot Air Solder Leveling) – najprostszy i najtańszy sposób wykończenia PCB. Polega na pobieleniu odsłoniętych części miedzi stopem lutowniczym typu cyna-ołów. Standardowo to stop zawierający ołów, ale w uzasadnionych przypadkach można zastosować HASL Lead Free, który zgodnie z nazwą nie zawiera ołowiu. Główną zaletą tego wykończenia jest niski koszt. Wadą – różnice w grubości wykończenia zależne od wielkości padów, mogące powodować trudności w lutowaniu małych komponentów lub zwarcia pomiędzy wyprowadzeniami układów.
- Immersion Tin – cynowanie chemiczne zapewnia płaską powierzchnię padów i dobrą lutowność. Główną wadą jest tu wrażliwość na zabrudzenia i zanieczyszczenia, które mogą utrudnić proces lutowania oraz proces technologiczny pozostawiający po sobie substancje szkodliwe dla środowiska.
- ENIG (Electroless Nickel/Immersion Gold) – chemiczna metoda pokrywania miedzi podkładową warstwą niklu, a następnie warstwą złota. Ta metoda zapewnia również płaską powierzchnię padów, doskonałą lutowność oraz wydłużony czas przechowywania obwodów elektronicznych. Wadę stanowi wysoki koszt produkcji.
- OSP (Organic Solderability Preservatives) – organiczna powłoka wykończeniowa zapewniająca płaską powierzchnię padów oraz dobrą lutowność. Wadą jest krótki okres przechowywania oraz szybka degradacja w procesie lutowania wieloprzebiegowego.
- Gold Fingers – specyficzny typ złocenia chemicznego stosowany w wypadku złącz krawędziowych, np. złącz kart rozszerzeń w komputerach. Taki typ charakteryzuje się dużą wytrzymałością mechaniczną, czyli odpornością na ścieranie. Gold Fingers zazwyczaj nanosimy na złącze, natomiast na pozostałej części PCB stosujemy inny typ platingu, na przykład ENIG.
Silkscreen – warstwa farby nanoszona na soldermaskę zwana również legendą lub warstwą opisową. Zazwyczaj występuje w kolorze białym. W wypadku gdy kolor soldermaski jest jasny, dla uzyskania lepszego kontrastu i czytelności oznaczeń stosowany jest silkscreen w kolorze czarnym. Informacje zawarte na warstwie opisowej to desygnatory i obrysy komponentów, oznaczenia polaryzacji, oznaczenia złącz czy logo producenta. Wykonanie legendy nie jest konieczne w produkcji PCB i zależy jedynie od decyzji klienta.
Panelizacja – standardowo obwody drukowane projektowane są w formie pojedynczej płytki. W celu maksymalnego wykorzystania materiału laminatu oraz optymalizacji montażu powierzchniowego lub przewlekanego pojedyncze PCB układane są jednak w macierz. Można wyróżnić dwa główne sposoby panelizacji – rylcowanie (nacięcie po obu stronach płyty) oraz frezowanie (obróbka kształtu płyty w panelu).
Fiduciale – to znaczniki technologiczne służące maszynom za punkty odniesienia na powierzchni PCB. Fiduciale mogą mieć różny kształt (koła, okręgi, kwadraty, krzyżyki, trójkąty), a ich rozmiar to zazwyczaj 1–1,5mm. Zaleca się, by fiduciale były umieszczone na obwiedni panelu, jak i na każdym obwodzie z osobna. Fiduciale powinny znajdować się po obu stronach PCB. Powinny również być oddalone od krawędzi panelu/PCB oraz od testpointów czy otworów o podobnych rozmiarach, mogących zostać zidentyfikowane przez maszyny jako fiduciale. Zazwyczaj umieszcza się fiduciale w trzech rogach panelu.
Jakie pliki są potrzebne w Comarch IoT Plant do złożenia zamówienia na płytki PCB?
– Podstawowymi plikami wymaganymi do zamówienia płytek PCB w Comarch IoT Plant są pliki Gerber. To one definiują wszystkie warstwy folii miedzianej, ich kształt, ścieżki, pady, ścieżkę frezowania lub rylcowania określającą kształt PCB oraz warstwy soldermaski, a także warstwy sitodruku – mówi Mateusz Rosek.
Bezpośrednio połączone z Gerberami są również pliki wierceń zawierające informacje na temat przelotek oraz otworów. Pliki te mogą być dostarczone osobno jako pliki każdej z warstw oraz wierceń dla otworów PTH i NPTH lub jako jedna paczka w formacie ODB++ lub tgz.
Kolejnym niezbędnym elementem dokumentacji potrzebnym do zamówienia PCB jest specyfikacja określająca liczbę i grubości warstw wymiary płytki, rodzaj materiału i wykończenia, a także sposób depanelizacji. W przypadku obwodów wielowarstwowych pomocne jest rozszerzenie specyfikacji o tak zwany stack-up, czyli graficzne lub tekstowe przedstawienie przekroju płytki zawierające grubości rdzenia, warstw miedzi i prepregów. W specyfikacji może być również zawarta informacja na temat docelowych wartości impedancji określonych ścieżek w obwodach wielowarstwowych.
Jeżeli klient nie precyzuje panelizacji w Gerberach, w Comarch IoT Plant wychodzimy z własną propozycją panelu zapewniającą optymalne ułożenie płytek PCB, co z kolei przekłada się na sprawny i poprawny montaż komponentów elektronicznych. Po zatwierdzeniu propozycji panelu przez klienta jest ona uwzględniana w zamówieniu PCB. Jeżeli panelizacja realizowana jest w formie mostków, do procesu depenalizacji niezbędna jest zawarta w Gerberach warstwa frezowania.
Na co zwracamy uwagę podczas weryfikacji projektu obwodów drukowanych?
Aby zapewnić sprawność procesów w Comarch IoT Plant, dokumentacja dostarczona przez klienta podlega zawsze weryfikacji naszych inżynierów. W wypadku gdy klient sam panelizuje płytkę PCB, sprawdzamy, czy panel może być obsłużony przez nasze maszyny. Ze względu na ograniczenia technologiczne staramy się, by wymiar panelu nie przekraczał wymiarów 350x300 mm. Czasami sugerujemy klientowi zmianę układu panelu, aby poprawić jego sztywność. Tyczy się to głównie szerokich paneli, gdzie jest dużo niewielkich płytek. Kolejną rzeczą, na jaką zwracamy uwagę, są różnego rodzaju złącza montowane blisko krawędzi PCB lub takie, które wychodzą poza obrys płytki. Tutaj w grę wchodzą trzy czynniki:
- Zastosowanie rylcowania przy jednoczesnym umieszczeniu złącz bezpośrednio przy krawędzi lub wystających poza obrys PCB uniemożliwiających depanelizację.
- Mostki znajdujące się zbyt blisko złącza lub bezpośrednio pod nim mogące utrudnić lub uniemożliwić depanelizację. Jeśli zachodzi taka potrzeba, rekomendujemy zmianę położenia mostków lub zmianę rodzaju panelizacji.
- Złącza posiadające na spodniej części obudowy wypustki pozycjonujące, które wymagają wykonania stosownych wycięć w laminacie PCB lub w obwiedni panelu.
W kolejnym kroku sprawdzamy położenie fiduciali – to punkt krytyczny z punktu widzenia wszystkich procesów realizowanych automatycznie na maszynach. Jeśli maszyna nie znajdzie bowiem punktu odniesienia, nie będzie mogła wykonać zaprogramowanych działań. Z tego względu jednym z naszych wymagań jest umieszczenie fiduciali po obu stronach panelu, w odległości minimum 4 mm od krawędzi zewnętrznej panelu.
Po zebraniu wszystkich uwag konsultujemy je z klientem w celu uzyskania optymalnej postaci panelu PCB.
Współpraca Comarch IoT Plant ze sprawdzonymi i niezawodnymi dostawcami PCB
Od wejścia na rynek udało nam się nawiązać współpracę z wieloma dostawcami PCB ofertującymi usługi na rynku światowym i europejskim. Dotychczasowa realizacja projektów urządzeń medycznych, wojskowych, a także kosmicznych pozwoliła zespołowi Comarch IoT Plant na kooperację z siecią dostawców oferujących najwyższą jakość. To podmioty wyspecjalizowane w realizacji trudnych projektów wielowarstwowych płytek, dysponujące dostępem do różnorodnych materiałów do zastosowań specjalistycznych, jak również spełniających określone, wyśrubowane normy.
– Od momentu przesłania zapytania ofertowego posiadamy pełne wsparcie przedstawicieli dostawców. Często już na tym etapie otrzymujemy cenny feedback z fabryki, która rekomenduje konkretne usprawnienia. Następnie jesteśmy prowadzeni przez etap pytań inżynierskich, gdzie uzgadniane są wszelkie szczegóły produkcji PCB – dodaje Mateusz Rosek.
Kluczowe elementy procesu: przechowywanie, defekty PCB oraz kontrola wejściowa płytek drukowanych
Po zakończeniu produkcji w fabryce płytki PCB są pakowane hermetycznie w woreczki próżniowe, zaopatrzone w pochłaniacze wilgoci i wskaźniki wilgotności. Pierwsze absorbują wilgoć zamkniętą w woreczkach podczas zgrzewania, drugie pozwalają stwierdzić, czy opakowanie nie uległo rozhermetyzowaniu podczas transportu.
– Wilgoć jest największym wrogiem obwodów drukowanych. Po pierwsze, w przypadku niektórych rodzajów wykończenia PCB, sprzyja powstawaniu korozji na powierzchni padów. Po drugie, może spowodować znacznie gorsze uszkodzenia płytki. Jeżeli wilgoć wniknie w strukturę płytki, może doprowadzić do napuchnięcia i rozwarstwienia laminatu – komentuje Mateusz Rosek.
Taki defekt może nie być widoczny od razu, niekiedy ujawnia się on dopiero podczas etapu lutowania, gdy w piecu pod wpływem wysokiej temperatury uwięzione w strukturze PCB drobinki wody zaczynają wrzeć, rozsadzając laminat. Tego rodzaju wady mogą pojawić się już na etapie produkcji laminatu, jeżeli materiał był składowany w niewłaściwy sposób, przez co arkusze włókna miały okazję nasiąknąć wilgocią.
Błędy w produkcji płytek PCB mogą zdarzyć się bez udziału wilgoci z powodu nieprawidłowego doboru ustawień procesu, w wyniku czego laminat zostanie niewłaściwie sprasowany i dojdzie do rozwarstwienia. Takie defekty są w większości przypadków wychwytywane przez kontrolę jakości w fabryce PCB, mimo to w Comarch IoT Plant po dostarczeniu do nas płytek sprawdzamy je pod kątem zgodności z projektem, a także ewentualnych uszkodzeń mechanicznych.
Comarch IoT Plant – montaż PCBA i dużo więcej
– Wykonując usługi montażu PCBA w Comarch IoT Plant, nowoczesnej hali produkcyjnej w samym sercu Krakowa, traktujemy obwody drukowane jako jeden z kluczowych komponentów w produkcji elektroniki, dlatego przykładamy ogromną wagę do zamawiania ich ze sprawdzonych źródeł, od zaufanych dostawców. Poddajemy je również szeregowi procesów kontrolnych, mając na uwadze finalny sukces projektu – mówi Mateusz Rosek.
Oferujemy naszym klientom wsparcie na każdym etapie tworzenia elektroniki – od pomysłu i prototypu aż po produkcję i testy urządzenia. W zakres usług IoT Plant wchodzi montaż powierzchniowy (SMT) i przewlekany (THT), w tym lutowanie zwykłe lub selektywne na fali oraz lutowanie ręczne. Zajmujemy się również odzyskiwaniem i naprawą elektroniki. W ramach badań jakości poddajemy ją szerokiemu spectrum testów: automatycznej kontroli optycznej (AOI) i RTG (AXI), testom funkcjonalnym ICT (In Circuit Test), FCT (Functional Tests), ICSP (In-Circuit Serial Programming), Flying Probe oraz środowiskowym.
Więcej o tym, jakie korzyści ze współpracy z naszą halą produkcyjną może zyskać Twoja firma, znajdziesz na stronie Comarch IoT Plant.