Prototypowanie urządzeń elektronicznych: Kluczowe wyzwania i jak je pokonać
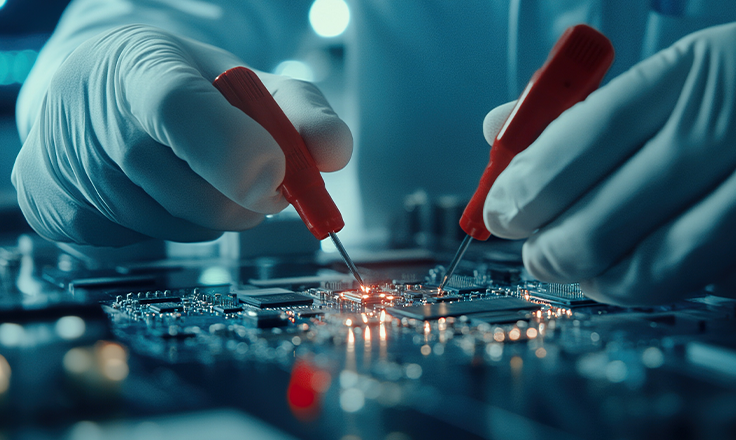
Prototypowanie urządzeń elektronicznych to jeden z najważniejszych etapów procesu projektowania – moment, w którym pomysł zaczyna nabierać realnych kształtów. To nie tylko testowanie technicznych założeń, ale także strategiczne działanie wymagające precyzyjnego planowania, optymalizacji i analizy funkcjonalności. Właśnie na tym etapie identyfikuje się potencjalne błędy, udoskonala poszczególne elementy i ocenia gotowość produktu do produkcji seryjnej. Niemniej jednak skuteczne prototypowanie nie jest wolne od wyzwań – od doboru odpowiednich komponentów po iteracyjne testy i integrację systemów.
W Comarch, dzięki wieloletniemu doświadczeniu w rozwoju technologii IoT, doskonale rozumiemy złożoność procesu prototypowania urządzeń elektronicznych i trudności, z którymi muszą mierzyć się inżynierowie. Wiemy również, jak im zaradzić.
Złożoność procesu projektowania
Tworzenie urządzeń elektronicznych to złożony proces, który obejmuje wiele etapów – od koncepcji, przez projektowanie układów PCB, aż po testowanie i optymalizację. Każdy z tych kroków wymaga precyzyjnego planowania i efektywnej współpracy między zespołami, aby uniknąć błędów i opóźnień. Złożoność procesu wynika z konieczności uwzględnienia wielu zmiennych na każdym etapie, takich jak wymagania techniczne, czy też koszty operacyjne.
Jak poradzić sobie z tą złożonością?
Pomocne może okazać się metodyczne podejście do projektowania, oparte na schematach blokowych i jasno określonych wymaganiach technicznych. Warto również uwzględnić aspekty takie jak efektywność energetyczna, miniaturyzacja oraz spełnianie norm bezpieczeństwa. Taki sposób działania pozwala na lepszą kontrolę procesu, skrócenie czasu opracowania gotowego produktu i minimalizację ryzyka popełnienia błędów na późniejszych etapach.
Dobór odpowiednich komponentów
Dobór odpowiednich komponentów to jeden z najważniejszych etapów prototypowania, który ma bezpośredni wpływ na funkcjonalność, niezawodność i trwałość urządzenia. Nieodpowiednio dobrane elementy mogą prowadzić do problemów z kompatybilnością, obniżonej wydajności oraz przyspieszonego zużycia, negatywnie wpływając na długoterminową niezawodność produktu. Istotne jest uwzględnienie wymagań technicznych, takich jak parametry elektryczne (prąd, napięcie), temperatura pracy czy wartości pojemności i oporu.
Jak zminimalizować ryzyko błędów?
Aby zminimalizować ryzyko błędów przy doborze komponentów, warto rozważyć ofertę renomowanych dostawców oraz skupić się na dokładnej analizie specyfikacji technicznych. Odpowiedni wybór komponentów zapewnia ich kompatybilność, wydajność oraz trwałość, tym samym zwiększając szanse na sukces prototypu.
Testowanie i walidacja prototypu
Przeprowadzenie szczegółowych testów prototypów w różnych warunkach eksploatacyjnych jest niezbędne do wykrycia potencjalnych usterek i zapewnienia ich niezawodności. Wczesne prototypy mogą różnić się formą od finalnego produktu, przez co skrywają błędy, które mogą zostać niezauważone bez odpowiednich procedur weryfikacyjnych.
Jak zapewnić dokładność testów i wykryć błędy na wczesnym etapie?
Wykorzystanie zaawansowanych narzędzi do testowania i symulacji pozwala na precyzyjną walidację wytrzymałości, kompatybilności i efektywności energetycznej prototypów. Należy testować zarówno pojedyncze komponenty, jak i całe systemy, aby ocenić ich funkcjonalność w warunkach zbliżonych do rzeczywistych. Wczesne wykrycie problemów i ich korekta znacząco zwiększają szansę na to, że urządzenia będą niezawodne, gdy trafią do produkcji seryjnej.
Integracja z procesem produkcyjnym
Przejście od prototypu do produkcji seryjnej to bardzo ważny etap, który wymaga nie tylko dopracowania samego projektu, ale także jego dostosowania do technologii produkcyjnych. Optymalizacja kosztów, wybór odpowiednich komponentów oraz zapewnienie zgodności z wymogami technologicznymi (np. SMT i THT) to wyzwania, które mogą wydłużyć proces wdrożenia i wpłynąć na jakość końcowego produktu.
Jak dostosować projekt do wymogów produkcji seryjnej?
Odpowiedzią jest tutaj współpraca z doświadczonymi partnerami zajmującymi się produkcją elektroniki (EMS — Electronics Manufacturing Services), która pozwala na precyzyjne dostosowanie projektów do wymagań technologicznych, zwiększenie efektywności procesu i zapewnienie, że produkty końcowe będą spełniać zarówno normy jakościowe, jak i założenia kosztowe. Dzięki temu projekty mogą być sprawnie wdrażane na szeroką skalę, bez kompromisów w zakresie funkcjonalności i niezawodności.
Czas i koszty
Ograniczenia budżetowe oraz presja czasu to jedne z najistotniejszych wyzwań w procesie prototypowania urządzeń elektronicznych. Wymagają one od inżynierów szybkiego podejmowania decyzji i kompromisów, które mogą negatywnie wpłynąć na jakość prototypu i całego procesu projektowania. Z jednej strony trzeba dążyć do optymalizacji kosztów, z drugiej — nie można pozwolić na pośpiech, który często prowadzi do błędów.
Jak skrócić czas realizacji i zoptymalizować koszty?
Aby zmniejszyć ryzyko, warto skorzystać z narzędzi, które umożliwiają szybkie testowanie i weryfikację rozwiązań przed ich wdrożeniem. Technologie takie jak druk 3D czy systemy CAD pozwalają na wczesne wykrywanie problemów i wprowadzenie poprawek, bez konieczności kosztownej produkcji próbnej. Dzięki nim można znacząco skrócić czas realizacji projektu i obniżyć koszty, zachowując kontrolę nad jakością. Co więcej, wdrożenie elastycznych rozwiązań produkcyjnych i metod zarządzania, takich jak lean management, pozwala na optymalizację procesów, minimalizując straty materiałowe i czasowe, a tym samym umożliwiając lepsze dostosowanie do budżetowych ograniczeń.
Usługi prototypowania w Comarch
Prototypowanie urządzeń elektronicznych to proces wymagający nie tylko znajomości technologii, ale także umiejętności zarządzania projektami, optymalizacji kosztów i szybkiego rozwiązywania problemów. Każdy etap, począwszy od projektowania, przez testy, aż po wdrożenie do produkcji, niesie ze sobą konkretne wyzwania, których umiejętne pokonanie decyduje o powodzeniu całego przedsięwzięcia.
W Comarch IoT Plant, dzięki doświadczeniu w IoT i inżynierii elektroniki, wypracowaliśmy metody pozwalające nie tylko skrócić czas realizacji, ale także zapewnić niezawodność i wysoką jakość produktu. Nowoczesne zaplecze produkcyjne, zaawansowany park maszynowy oraz elastyczne podejście do technologii SMT i usług EMS sprawiają, że możemy wspierać firmy na każdym etapie procesu – od koncepcji po produkcję seryjną.
Poszukujesz partnera technologicznego w procesie prototypowania? Postaw na doświadczenie i sprawdzone rozwiązania oferowane przez Comarch IoT Plant.